Saiken Pump Industry will explain to you how to choose seals for gear pumps:
The principle of selection of gear oil pump seals is that for occasions with low requirements, they can be selected based on experience and replaced when they are not suitable. But for those occasions with strict requirements, such as explosive, highly toxic and flammable gas and strongly corrosive liquid equipment, reaction tanks and pipeline systems, etc., it should be based on the working pressure, working temperature, corrosiveness of the sealing medium and the combined sealing surface The form of choice. Generally speaking, at room temperature and low pressure, use non-metallic soft honey gasket; at medium pressure and high temperature, use metal and non-metal combination gasket or metal gasket; when temperature and pressure have large fluctuations, use good elasticity Or self-tightening gasket; in low temperature, corrosive media or vacuum conditions, gaskets with special properties should be considered. What needs to be explained here is the influence of flange conditions on gasket selection.
The influence of flange form. Different flange forms require different gaskets. Smooth-faced flanges are generally only used for low pressure and are equipped with soft thin gaskets; under high pressure, if the strength of the flange is sufficient, smooth-faced flanges can also be used, but thick soft gaskets or in-belt reinforcement should be used Ring or reinforced ring wound gasket. In this case, metal gaskets are also not suitable, because the required pressing force is too large at this time, resulting in greater deformation of the bolts and making the flange difficult to seal. If a metal gasket is to be used, the smooth surface should be reduced to reduce the contact area with the gasket. In this way, under the same bolt tension, the compressive stress of the narrow and smooth surface after reduction will increase.
The influence of flange surface roughness. The flange surface roughness has a great influence on the sealing effect, especially when non-soft gaskets are used, the large value of the sealing surface roughness is one of the main reasons for leakage. For example, the knife pattern of the turning flange surface is a spiral line. When using a metal gasket, if the roughness value is large, the gasket cannot block the spiral groove formed by the knife pattern. Under pressure, the medium will Leaked along this groove. The soft gasket has much lower requirements for the smoothness of the flange surface. This is because it is easy to deform and can block the processing knife lines, thereby preventing leakage. For soft gaskets, the flange surface is too smooth to be unfavorable because the interface leakage resistance is reduced at this time. Therefore, different gaskets require different flange surface roughness.
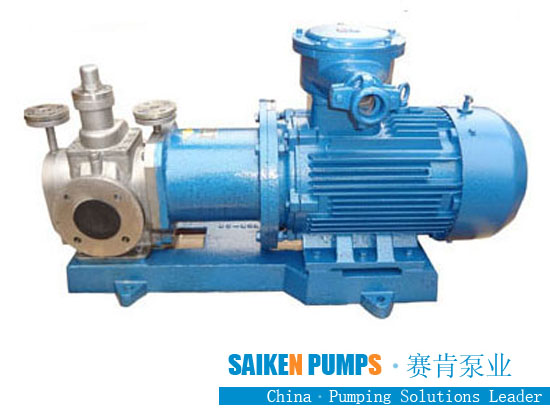