In the production or selection, how to make KCB gear oil pump energy-saving measures mainly include the following 4 points.
(1) Select the appropriate model of KCB gear oil pump to correctly calculate the flow and head required by the pipeline, and make the rated flow and head of the selected pump equal to or slightly larger than the flow and head required by the pipeline, so that the KCB gear oil pump is in Work in efficient areas. The larger the flow and head margin of the KCB gear oil pump, the lower the working efficiency.
(2) Reduce the resistance of the pipeline and reduce the required head of the pipeline. From Bernoulli's equation, the head of the pump required by the pipeline is the first term (Z2-Z,) and the second term is determined by the working conditions. Decided, item 3 is determined by the structure of the pump and cannot be changed at will. If you want to reduce the required pump head date, you can only consider from the fourth item bi. The main feasible measures to reduce pipeline resistance are: appropriately increase the diameter of the pipe: avoid installing unnecessary valves, instruments, etc.; the pipeline should be as straight as possible, with fewer turns; use a pipe with a smooth inner surface; timely remove the pipeline Sundries and scaling, etc. When the resistance of the pipeline drops, the pump head required by the pipeline also drops, thereby reducing the power consumption of the pump.
(3) Improve the structure of the impeller, improve the function of the impeller, improve the structure of the pump body, and reduce the fluid energy loss in the KCB gear pump. The purpose of improving the structure of the impeller is to improve the flow of the liquid in the impeller, so that the flow is stable, there is no vortex, and the impact loss and friction loss are reduced to a minimum. Theoretically, the more blades of the impeller, the smaller the thickness of the blades, the higher the efficiency of the impeller's work on the liquid. However, the more blades, the narrower the flow passage area of the liquid in the impeller, the greater the resistance when the fluid passes through the impeller: the smaller the thickness of the blade, the lower the strength of the blade, the easier it is to damage, and the more difficult it is to manufacture. The idea to solve this problem lies in: in the case of normal use, it is necessary to ensure that there is enough flow channel area in the impeller, and to appropriately increase the number of blades.
The internal leakage of the KCB gear oil pump and the unevenness of the inner surface of the pump casing are also a cause of energy loss. For this reason, it is necessary to replace the excessively worn population seal ring in time to reduce internal leakage. Polish the runner to make the guide surface of the runner smooth and reduce the oil loss in the pump. Remove blockages such as sand, stone and cast iron residues in the pump.
(4) Reduce the diameter of the impeller and reduce the speed of the impeller. When the flow and head of the pump are large and there is no more suitable pump available, you can use the impeller, reduce the outer diameter of the impeller, or reduce the impeller. The method of rotating speed can achieve the purpose of reducing the shaft power of the pump and reducing power consumption. After the outer diameter of the impeller is cut, or the speed of the impeller is reduced, the shaft power of the pump drops quickly.
It should be proposed that after the impeller is cut or the speed is reduced, because the shaft power is reduced, a motor with a smaller power should be replaced. Otherwise, it is difficult to achieve the purpose of energy saving.
In addition, strictly implementing the assembly technical requirements of KCB gear pumps, maintaining good running performance, strengthening routine maintenance, and replacing excessively worn parts in time are also important measures for energy saving KCB gear oil pumps.
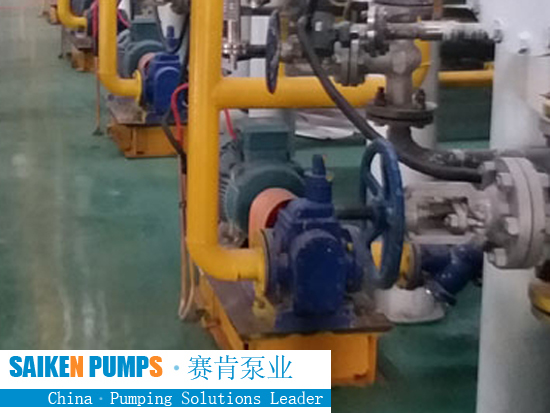