Due to the structural limitation of the fixed displacement, it is generally considered that the gear pump can only be used as a constant flow hydraulic source. However, the accessory and screw connection combination valve solution is effective for improving its function, reducing system cost and improving system reliability. Therefore, the performance of the gear pumps can approach the expensive and complex plunger pump. Installing the control valve directly on the pump can save the pipeline between the pump and the directional valve, thereby controlling the cost. Fewer pipes and connections can reduce leakage, thereby improving work reliability. In addition, the valve installed in the pump can reduce the circulation pressure of the circuit and improve its working performance.
The unloading element will combine a large flow pump with a small power single pump. The liquid is discharged from the outlets of the two pumps until a predetermined pressure and/or flow rate is reached. At this time, the high-flow pump circulates the flow from its outlet to its inlet, thereby reducing the pump's output flow to the system, that is, reducing the pump power to slightly higher than the value required for the high-pressure part. The percentage of flow reduction depends on the ratio of unloaded displacement to total displacement at this time. The combination or threaded connection unloading valve reduces or even eliminates pipelines, holes, accessories and other possible leakage. Manually operated unloading elements are often used in circuits that require a large flow rate for rapid action and a large flow rate for rapid action, and reduce flow rate for precise control, such as a fast telescopic boom circuit. When the unloading valve of the circuit has no control signal (left position), the circuit always outputs a large flow. For a normally open valve, the loop will output a small flow under normal conditions.
Pressure sensing unloading valve is the most common solution. The spring action keeps the unloading valve in its high flow position (left position). When the circuit pressure reaches the preset value of the overflow valve, the overflow valve opens, and the unloading valve switches to its low flow position (right position) under the action of hydraulic pressure. The pressure sensing unloading circuit is mostly used for hydraulic cylinders that need to be fast during the stroke and high pressure and low speed at the end of the stroke. The pressure sensing unloading valve base is basically an automatic unloading component that can be unloaded when the system pressure is reached. It is commonly used in the splitter of the speed measuring instrument and the hydraulic vise. The unloading valve in the flow sensing unloading circuit is also pressed to the large flow position (left position) by a spring. The size of the fixed orifice in the valve is determined by the flow required for the optimal engine speed of the equipment. If the engine speed exceeds this optimal range, the pressure drop of the throttle orifice will increase, thereby shifting the unloading valve to the low flow position (right position). Therefore, the adjacent components of the high-flow pump are made into a size that can throttle the maximum flow, so the circuit has low energy consumption, stable operation and low cost. The typical application of this circuit is to limit the circuit flow rate to an optimal range to improve the performance of the entire system, or to limit the circuit pressure during high-speed machine driving. Often used in garbage trucks.
Regardless of the pump speed, working pressure or the flow rate required by the branch, a fixed-value primary flow control valve can always ensure the flow required for the equipment to work. The output flow of the pump must be greater than or equal to the flow required by the primary oil circuit, and the secondary flow can be used for other purposes or return to the tank. The fixed-value primary flow valve (proportional valve) combines primary control with the hydraulic pump, eliminating pipelines and eliminating external leakage, thus reducing costs. The typical application of this gear pump china circuit is the steering mechanism often seen on truck cranes, which eliminates a pump. The function of the load-sensing flow control valve is very similar to that of a fixed-value primary flow control: that is, no matter the pump speed, working pressure, or branch pumping demand flow, it provides a primary flow. Only provide the required flow to the primary oil circuit through the primary oil port until its maximum adjustment value. This loop can replace the standard primary flow control loop to obtain the maximum output flow. Because the pressure of the no-load loop is lower than the fixed value primary flow control scheme, the loop temperature rise is low and the no-load power consumption is small. The load-sensing proportional flow control valve is the same as the primary flow control valve, and its typical application is power steering.
Regarding bypass flow control, regardless of the pump speed or working pressure, the pump always supplies liquid to the system at a predetermined maximum value, and the excess is discharged back to the tank or the inlet of the pump. This program limits the flow into the system to make it have the best performance. The advantage is that the maximum adjustment flow can be controlled by the loop scale to reduce costs; the pump and valve are combined into one, and the bypass control of the pump minimizes the loop pressure, thereby reducing the pipeline and its leakage. The bypass flow control valve can be designed together with the middle group load sensing control valve that limits the working flow (working speed) range. This type of gear pump circuit is often used in garbage trucks or power steering pump circuits that limit hydraulic operation to make the engine reach the best speed, and can also be used in stationary machinery.
The dry suction valve is an air-controlled hydraulic valve, which is used for pumping oil throttling. When the hydraulic pressure of the equipment is empty, only a very small flow (<18.9t/min) is passed through the pump; and when there is a load, Full flow suction pump. This kind of circuit can save the clutch between the pump and the prime mover, thereby reducing the cost, and also reducing the no-load power consumption, because the extremely small flow through the loop maintains the prime mover power of the equipment. In addition, it also reduces the noise of the pump at no load. The dry suction valve circuit can be used for on-off hydraulic systems in any vehicle driven by an internal combustion engine, such as garbage trucks and industrial equipment.
At present, the working pressure of gear pumps is close to that of plunger pumps, and the combined load sensing scheme provides variable possibilities for gear pumps. One of the decisive factors for a reasonable selection of hydraulic pump schemes is the cost of the entire system. Compared with expensive plunger pumps, gear pumps are characterized by their lower cost, simple circuit, and low filtration requirements.
Gear pump manufacturers and suppliers from China
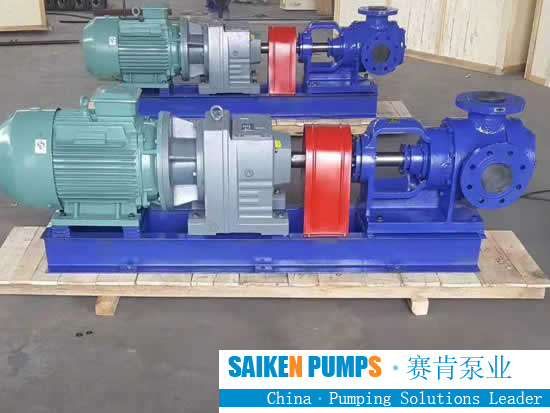