When NYP high-viscosity rotor pumps transport high-viscosity media, it is often necessary to reduce the use of speed or manual speed and automatic speed control to control the actual flow of NYP high-viscosity rotor pumps to meet the production needs of the process. How to set up and use variable-frequency NYP high-viscosity rotor pumps, Some precautions in use, the following engineers of Saiken Pump Industry will give you a detailed explanation.
Generally speaking, NYP high viscosity rotor pumps achieve speed reduction. The commonly used methods include gear speed motors, gearbox deceleration, frequency conversion motors, manual stepless speed motors, electromagnetic debugging, etc. Frequency conversion motors use "special frequency conversion induction motors+ The "frequency converter" AC speed regulation method, coupled with the electrical automatic control system, greatly improves the degree of mechanical automation and production performance, saves energy, improves the product qualification rate and product quality, the power system capacity increases accordingly, and the equipment is miniaturized and increased. For comfort, variable frequency speed regulation has now become the mainstream speed regulation scheme, which can be widely used in the continuously variable transmission of the pump industry. At present, NYP high-viscosity rotor pumps, high-viscosity roots pumps, single screw pumps, vacuum discharge gear pumps and variable frequency motors are relatively common among deceleration devices. For customers who require NYP high-viscosity rotor pumps to have a fixed flow rate, it is recommended to use gear reducer motors and cycloidal pin gear motors. If customers require NYP high-viscosity rotor pumps to require adjustable flow during the delivery process, then it is recommended to choose a stepless speed motor or Inverter motor, at the same time, the power requirement of the selected motor when selecting the inverter motor is higher than that of the standard configuration. It can prevent the inverter motor from damaging the motor when the NYP high viscosity rotor pump is started.
Application category of inverter motor:
1: Insulation grade, generally F grade or higher, increase the insulation strength to the ground and the turns, especially the ability to withstand the impulse voltage of the insulation.
2: For the vibration and noise of the motor, the rigidity of the motor components and the whole should be fully considered, and the natural frequency should be increased as much as possible to avoid the resonance phenomenon with each force wave.
3: Cooling method: usually forced ventilation cooling, that is, the main motor cooling fan is driven by an independent motor.
4: Measures to prevent shaft current, bearing insulation measures should be adopted for motors with a capacity exceeding 160KW. The main reason is that the asymmetry of the magnetic circuit is likely to occur, and the shaft current will also be generated. When the currents generated by other high-frequency components are combined together, the shaft current will increase greatly, resulting in damage to the bearing, so insulation measures are generally taken.
5: For constant power frequency conversion motors, when the speed exceeds 3000r/min, special high temperature resistant grease should be used to compensate for the increase in bearing temperature.
Especially with the increasingly widespread application of frequency converters in the field of industrial control, the use of frequency conversion motors is also becoming more and more widespread. It can be said that due to the superiority of frequency conversion motors in frequency conversion control over ordinary motors, wherever we use frequency converters, we It is not difficult to see the figure of inverter motor.
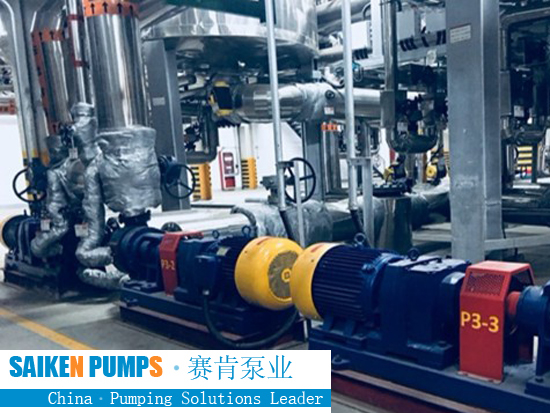