Before starting operation, fill the housing of the SS high-viscosity gear pump with the liquid to be transported to facilitate safe start-up. If the ambient temperature is lower than the freezing point, hot steam should be introduced into the pump in advance to perform pre-heat treatment before the rotor pump can be started. The rotation direction of the rotor pump should be consistent with the inlet and outlet. The support or flange of the high-viscosity gear pump and its drive motor should use a common installation foundation. The foundation, flange or support must have sufficient rigidity to reduce the vibration and noise generated when the rotor pump is running. The motor and the rotor pump must be connected by an elastic coupling, and the coaxiality is less than 0.1 mm. The inclination angle shall not be greater than 1 degree, and it shall not be hit with a hammer when installing the coupling, so as not to damage the gears and other parts of the SS high viscosity pump. If driven by pulleys, sprockets, etc., brackets should be provided to prevent the driving gear bearings from being subjected to radial forces. A safety valve and other protective devices should also be installed on the outlet pipe of the high-viscosity pump, so that once the outlet channel of the pump is blocked, the safety valve can be opened to relieve the pressure.
When tightening the anchor screws of high-viscosity pumps and motors, the force of the screws should be even and the connection is reliable. When rotating the coupling by hand, you should feel that the rotor pump can easily rotate, and there is no abnormal phenomenon such as jamming before you can pipe. The inner diameter of the oil suction pipe of the high viscosity pump should be large enough, and avoid narrow channels or sharp bends, reduce elbows, remove unnecessary valves and accessories, reduce the installation height of the pump as much as possible, shorten the length of the oil suction pipe to reduce pressure loss . The sealing of pipe joints and other components should be good to prevent air intrusion and thus control the occurrence of cavitation and cavitation. If the high-viscosity pump is run for the first time, or used after a long period of inactivity, it is best to run it for about an hour under no-load or light-load conditions. If abnormal temperature rise, leakage, vibration and noise are detected in advance during the running-in phase, the machine should be shut down for inspection. The rotor pump and the drive motor should be connected through a flexible coupling and installed on the same bottom plate to ensure coaxiality. The bottom plate is installed on an elastic support to further improve the vibration isolation effect.
In high-viscosity pumps, the inner rotor is the driving wheel and the outer rotor is the driven theory. Since the number of teeth of the inner and outer rotors differs by one tooth, there is secondary engagement during the meshing process, which will form several independent closed liquid-containing chambers. As the inner and outer rotors mesh and rotate, the volume of each liquid chamber changes differently: when the volume of the liquid chamber changes from small to large, a partial vacuum is generated in the liquid chamber, and under the action of atmospheric pressure, the liquid passes through the inlet pipe and the pump The annular groove on the cover enters the pump cavity and starts to suck liquid, when the volume of the liquid chamber reaches the maximum. The aspiration process is over; when the volume in the liquid chamber changes from large to small. The liquid in the liquid-filled chamber is pressed out from the other annular groove, which is the pumping process. During the operation of the internal gear pump, when the inner and outer rotors run in the same direction at different speeds around two parallel axes, relative motion must occur. This movement creates a constantly changing space between the inner and outer rotors, which is connected to the suction and discharge channel to achieve the purpose of suction and discharge.
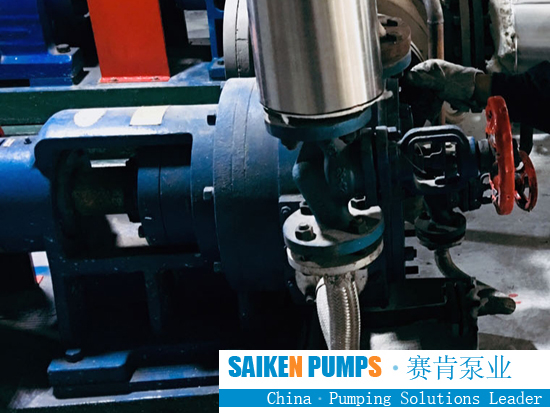